PORTABLE DESIGN
With its versatility, ease of installation, and flexibility to accommodate varied in situ machining conditions, LMD5000 series have gained significant traction across different field. They offer unique advantages such as mobility, affordability and scalability, making them a valuable tool for enterprise looking for efficient and economical machining options.
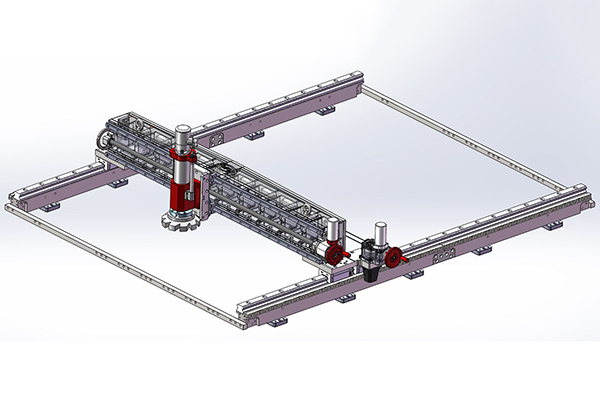
Gantry Milling Mode
Range: 5000*5000mm
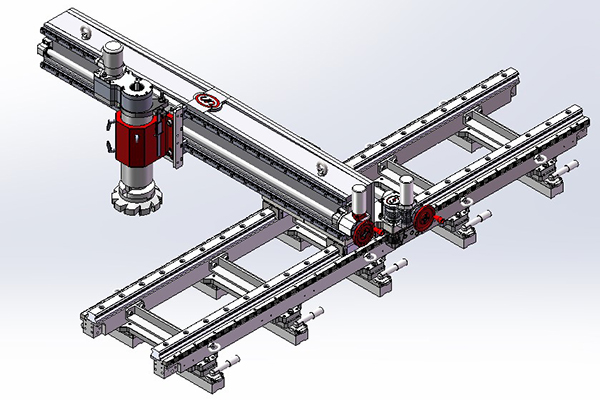
Line Milling Mode
Range: 5000mm